ബെയറിംഗ് വ്യവസായത്തിൽ, റിംഗ് ഫ്രാക്ചർ ഗോളാകൃതിയിലുള്ള റോളർ ബെയറിംഗുകളുടെ ഗുണനിലവാര പ്രശ്നം മാത്രമല്ല, എല്ലാത്തരം ബെയറിംഗുകളുടെയും ഗുണനിലവാര പ്രശ്നങ്ങളിൽ ഒന്നാണ്. ബെയറിംഗ് റിംഗ് ഒടിവിൻ്റെ പ്രധാന രൂപം കൂടിയാണിത്. കാരണം പ്രധാനമായും ബെയറിംഗിൻ്റെ അസംസ്കൃത വസ്തുക്കളുമായി ബന്ധപ്പെട്ടിരിക്കുന്നു. പിന്നീടുള്ള ഘട്ടത്തിൽ അനുചിതമായ പ്രവർത്തനവുമായി ബന്ധപ്പെട്ട ബന്ധം, ഉപകരണങ്ങളുടെ പ്രവർത്തന സമയത്ത് ഫെറൂൾ ബ്രേക്കേജ് പോലുള്ള പ്രശ്നങ്ങൾക്ക് കാരണമാകും. അത് എങ്ങനെ തടയാം? നമുക്ക് ഒരുമിച്ച് നോക്കാം:
1. ഒന്നാമതായി, ഗോളാകൃതിയിലുള്ള റോളർ ബെയറിംഗുകൾ നിർമ്മിക്കുന്നതിനുള്ള അസംസ്കൃത വസ്തുക്കൾ കർശനമായി നിയന്ത്രിക്കുക, പ്രത്യേകിച്ച് പ്രോസസ്സിംഗ് സമയത്ത്, ഞങ്ങൾ പൊട്ടുന്ന ഘടകങ്ങൾ, കാർബൈഡ് ദ്രാവക വേർതിരിവ്, മെഷ്, ബെൽറ്റ്, അസംസ്കൃത വസ്തുക്കളിൽ അടങ്ങിയിരിക്കുന്ന മറ്റ് ഘടകങ്ങൾ എന്നിവ ഒഴിവാക്കണം. ഈ ഘടകങ്ങൾ ഇല്ലാതാക്കിയില്ലെങ്കിൽ, അത് സമ്മർദ്ദ ഏകാഗ്രതയ്ക്ക് കാരണമാകും, വളയത്തിൻ്റെ അടിസ്ഥാന ബലം സാവധാനം ക്ഷയിപ്പിക്കും, കഠിനമായ സന്ദർഭങ്ങളിൽ ഗോളാകൃതിയിലുള്ള റോളർ ബെയറിംഗിൻ്റെ മോതിരം നേരിട്ട് തകരാൻ ഇടയാക്കും. ഇവിടെ, സ്ഫെറിക്കൽ റോളർ ബെയറിംഗ് നിർമ്മാതാക്കൾ, സ്ഥിരതയുള്ളതും വിശ്വസനീയവുമായ സ്റ്റീൽ വാങ്ങാൻ എല്ലാവരും ശ്രമിക്കണമെന്ന് നിർദ്ദേശിക്കുന്നു, കൂടാതെ സ്റ്റീലിൻ്റെ സംഭരണം പതിവായി പരിശോധിക്കുകയും ഉറവിടത്തിൽ നിന്ന് നിയന്ത്രിക്കുകയും ചെയ്യുക, അങ്ങനെ പിന്നീടുള്ള ഉപയോഗം മികച്ചതായി ഉറപ്പാക്കുക.
2. ഗോളാകൃതിയിലുള്ള റോളർ ബെയറിംഗുകളുടെ ഉൽപാദന പ്രക്രിയയിൽ അമിതമായി കത്തുന്നത്, അമിതമായി ചൂടാകൽ, ആന്തരിക വിള്ളലുകൾ എന്നിവ ഉണ്ടാകുകയാണെങ്കിൽ, അത് പൊതുവെ, പ്രോസസ്സിംഗ് സമയത്ത് കെട്ടിച്ചമയ്ക്കുമ്പോൾ താപനില നിയന്ത്രണം വേണ്ടത്ര സ്ഥിരതയില്ലാത്തതാണ്, ഇത് ഫെറൂളിൻ്റെ കാഠിന്യവും ശക്തിയും കുറയുന്നതിന് കാരണമാകുന്നു. . അതിനാൽ, അത്തരം കാര്യങ്ങൾ ഒഴിവാക്കാനും തടയാനും, കൃത്രിമമായതിനുശേഷം പ്രോസസ്സിംഗ് താപനില, ചാക്രിക ചൂടാക്കൽ, താപ വിസർജ്ജനം എന്നിവ കർശനമായി നിയന്ത്രിക്കേണ്ടത് ആവശ്യമാണ്. ഇവിടെ, ഉരുണ്ട റോളർ ബെയറിംഗ് നിർമ്മാതാക്കൾ ചൂട് ഇല്ലാതാക്കാൻ സ്പ്രേ കൂളിംഗ് ഉപയോഗിക്കാമെന്ന് ശുപാർശ ചെയ്യുന്നു, പ്രത്യേകിച്ച് വലിയ സ്വയം വിന്യസിക്കുന്ന റോളർ ബെയറിംഗുകൾക്ക്. റോളർ ബെയറിംഗ് വളയങ്ങൾക്ക് വ്യക്തമായ ഇഫക്റ്റുകൾ ഉണ്ട്. ഇവിടെ, 700 ഡിഗ്രി സെൽഷ്യസിനു മുകളിലുള്ള താപനില കഴിയുന്നത്ര നിയന്ത്രിക്കാൻ ശ്രദ്ധിക്കേണ്ടത് ആവശ്യമാണ്, കൂടാതെ ഒരു ഇനവും ചുറ്റും സൂക്ഷിക്കരുത്.
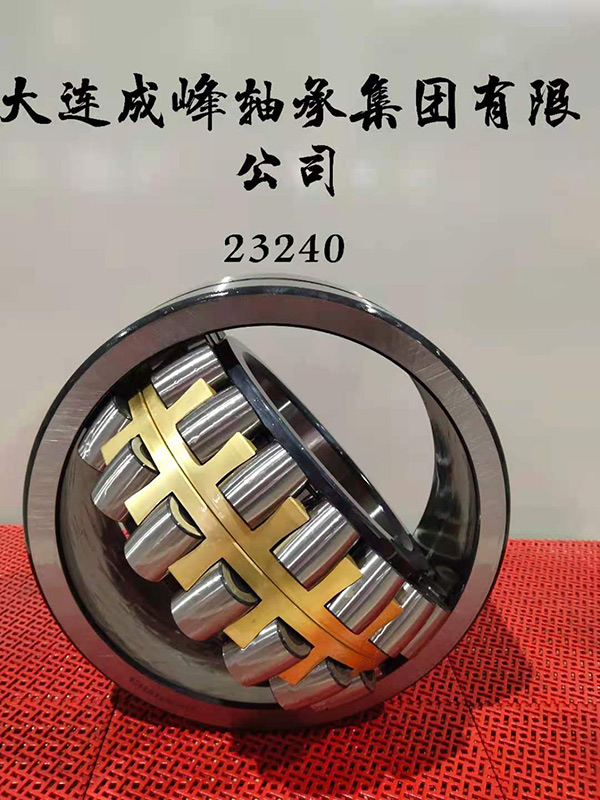
3. പ്രോസസ്സിംഗ് പ്രക്രിയയിൽ ചൂട് ചികിത്സ നടത്തുന്നത് വളരെ പ്രധാനമാണ്. ടെസ്റ്റിംഗ് ഉപകരണങ്ങളുടെ വിശ്വാസ്യത ശ്രദ്ധിക്കുക. പ്രോസസ്സ് ചെയ്യുന്നതിന് മുമ്പ് ഇത് മുൻകൂട്ടി പരിശോധിക്കേണ്ടതാണ്. അളക്കൽ ഡാറ്റയുടെ വിശ്വാസ്യത ഉറപ്പാക്കാൻ പരിശോധനയ്ക്കിടെ കർശനമായ പരിശോധന നടത്തുന്നു. തെറ്റായ രേഖകളും ക്രമരഹിതതയും, മുഴുവൻ ഹീറ്റ് ട്രീറ്റ്മെൻ്റ് പ്രക്രിയയിലും ഫെറുളിൽ നിന്ന് ഗോളാകൃതിയിലുള്ള റോളറിൻ്റെ ഗുണനിലവാരത്തിൻ്റെ ഗ്യാരണ്ടിയും ഇതിന് കാരണമാകുന്നു. പരിശോധനയ്ക്ക് പുറമേ, ശമിപ്പിക്കുന്ന പ്രക്രിയയുടെ അവസ്ഥകൾ കൂടുതൽ മെച്ചപ്പെടുത്തണം. വലിയ ഗോളാകൃതിയിലുള്ള റോളർ ബെയറിംഗ് വളയങ്ങളുടെ തകരാറുകൾ പരിഹരിക്കുന്നതിനാണ് ഇത്. ശമിപ്പിക്കുന്ന എണ്ണയുടെ ഘടനയും പ്രകടനവും മുൻകൂട്ടി നിശ്ചയിക്കണം, അത് ആവശ്യകതകൾക്ക് അനുസൃതമായി കർശനമായി ഉപയോഗിക്കുകയും ദ്രുതഗതിയിലുള്ള കെടുത്തൽ എണ്ണ ഉപയോഗിച്ച് മാറ്റിസ്ഥാപിക്കുകയും വേണം. ശമിപ്പിക്കുന്ന സാഹചര്യങ്ങൾ മെച്ചപ്പെടുത്തുന്നതിന് ശമിപ്പിക്കുന്ന മാധ്യമം മെച്ചപ്പെടുത്തുക.
4. ഫിനിഷ്ഡ് സ്ഫെറിക്കൽ റോളർ ബെയറിംഗ് റിംഗിനായി, ഗ്രൈൻഡിംഗ് പൊള്ളലുകളും വിള്ളലുകളും അനുവദനീയമല്ല, പ്രത്യേകിച്ച് അകത്തെ റിംഗ് സ്ക്രൂഡ്രൈവറിൻ്റെ പൊരുത്തപ്പെടുന്ന ഉപരിതലത്തിൽ പൊള്ളലേറ്റതിന് അനുവദനീയമല്ല, അതിനാൽ അച്ചാർ ചെയ്തതിന് ശേഷം ഇത് സാധാരണയായി ആവശ്യമാണ്. കർശനമായ പരിശോധന നടത്തുകയും കേടായ ഉൽപ്പന്നങ്ങൾ തിരഞ്ഞെടുക്കുകയും വേണം. നന്നാക്കാൻ കഴിയാത്ത ചില ഗുരുതരമായ പൊള്ളലുകൾ ഉടനടി നീക്കം ചെയ്യണം. കത്തിച്ച ഫെറൂളുകൾ ഉപകരണങ്ങളിൽ ഇടാൻ പാടില്ല.
5. ഗോളാകൃതിയിലുള്ള റോളർ ബെയറിംഗുകൾ തിരിച്ചറിയുന്നതിന് കർശനമായ മാനദണ്ഡങ്ങളും ഉണ്ട്. വാങ്ങിയ ഉരുക്ക് സ്റ്റോറേജിൽ ഇടുമ്പോൾ, അത് GCr15 ഉം GCr15SiMn ഉം തമ്മിൽ കർശനമായി വേർതിരിക്കേണ്ടതാണ്, രണ്ട് വ്യത്യസ്ത മെറ്റീരിയലുകളും ഉൽപ്പന്നങ്ങളും.
വിവരങ്ങളുടെ ഒരു ഭാഗം ഇൻറർനെറ്റിൽ നിന്നാണ് വരുന്നത്, സുരക്ഷിതവും സമയബന്ധിതവും കൃത്യവുമാകാൻ ശ്രമിക്കുന്നു. കൂടുതൽ വിവരങ്ങൾ കൈമാറുക എന്നതാണ് ഉദ്ദേശ്യം, അത് അതിൻ്റെ വീക്ഷണങ്ങളോട് യോജിക്കുന്നുവെന്നോ അതിൻ്റെ ആധികാരികതയ്ക്ക് ഉത്തരവാദിയാണെന്നോ അർത്ഥമാക്കുന്നില്ല. ഈ വെബ്സൈറ്റിലെ വീണ്ടും അച്ചടിച്ച വിവരങ്ങളിൽ പകർപ്പവകാശവും മറ്റ് പ്രശ്നങ്ങളും ഉൾപ്പെടുന്നുവെങ്കിൽ, അത് ഇല്ലാതാക്കാൻ കൃത്യസമയത്ത് ഈ വെബ്സൈറ്റുമായി ബന്ധപ്പെടുക.
പോസ്റ്റ് സമയം: ജൂലൈ-25-2022